Data Transformation: From Reactive to Predictive Maintenance
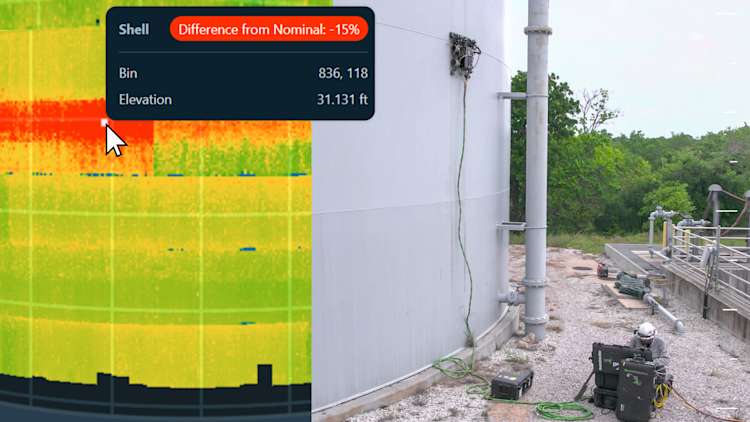
With large industrial equipment comes inherent risks and costly consequences when something goes wrong. Asset failures can send devastating ripple effects, causing unplanned downtime, lost productivity and revenue, significant unbudgeted costs, and dangerous safety incidents.
Maintenance activities are critical to running operations safely, reliably, and seamlessly across various industrial sectors. The ultimate goal of performing maintenance is to maximize the availability of assets while mitigating or fixing issues.
Though this primary goal remains, how we approach maintenance has drastically evolved. Facilities have shifted from trying to figure out what happened after something fails to predicting what will happen, when it will happen, and what proactive actions can be taken to avoid problems.
In this blog, we dive into three different approaches to maintenance – reactive, preventive, and predictive – and discuss how data is changing the game as companies advance with Industry 4.0 digital transformation.
What is Reactive Maintenance?
Reactive maintenance is the most simplistic form and oldest approach to maintaining assets and equipment. With this approach, companies perform maintenance work after a failure occurs to restore the asset to its operational condition. Information is used to figure out what went wrong. While getting to the root cause can be helpful, the damage is already done.
As assets age, risks increase over time. Without regular maintenance and monitoring, an asset’s usable life is reduced, leading to more frequent repairs and replacements. Reactive maintenance may save time and investment upfront, but companies will likely pay the price later.
Reactive maintenance often leads to additional unplanned downtime, which costs industrial manufacturers an estimated $50 billion annually. A study from the National Institute of Standards and Technology stated that manufacturing plants that rely on reactive maintenance experience 53% more downtime, 79% more defects in manufactured products, and 49% more lost sales compared to plants using preventive or predictive maintenance.

In addition to lost productivity and profits, the cost of repairs, labor, and parts often increases when maintenance work is unplanned. Resources become strained to fix issues and resume production as quickly as possible to reduce downtime windows.
At first glance, reactive maintenance may seem like the easy, simple route. However, this approach can quickly become dangerous, time intensive, and expensive.
What is Preventive Maintenance?
Instead of waiting until a failure happens to take action, preventive maintenance takes a more proactive approach. Preventive maintenance plans can include inspections, routine maintenance, part replacements, and other pre-planned activities that are performed based on time intervals or equipment usage. For example, a facility may replace a particular part after 1,000 hours of use or perform a service check on a particular asset biannually.
This approach aims to reduce unplanned downtime by keeping equipment in good working order, anticipating potential issues, and resolving problems before a failure occurs. This method requires planning and scheduling of maintenance before issues become known, making it important to keep accurate records of inspections and service reports. These routine maintenance practices can help sustain or extend the useful life of an asset by keeping degradation at an acceptable level.
Preventive maintenance can make facilities safer and increase asset reliability while reducing failures, costs, and downtime. However, facilities often prematurely replace assets or perform unneeded maintenance when following a time-based maintenance schedule. Companies waste time, money, and resources when there isn’t a clear picture of asset health.
At the same time, underlying damage mechanisms could be present and go unnoticed. If a facility only focuses on the scheduled tasks in its preventive plan, asset owners may overlook dangerous degradation below the surface, leaving significant issues unaddressed.
What is Predictive Maintenance?
Predictive maintenance takes preventive measures to the next level. Rather than performing maintenance activities based on a preset schedule, predictive maintenance leverages deep data insights about the asset's condition to predict failures, determine priorities, estimate remaining asset life, and plan when action needs to be taken.
Industry 4.0 technologies are bridging the physical and digital worlds to quickly and easily identify potential problems before they become apparent. Advanced technologies, including robotics and sensors, collect robust amounts of data about assets and equipment to create a full health scan. The raw data feeds into an analytics software platform to create useful dashboards and models with actionable insights.
Interactive data visualizations in the platform can help estimate the remaining life of assets and pinpoint when and where targeted repairs are needed to improve the reliability and longevity of assets. This insight empowers facilities to optimize maintenance schedules, resources, processes, and CapEx. With a complete understanding of asset health, resources can be procured to maximize budgets and time, with work conducted strategically to minimize downtime.
Using digital twins, companies can evaluate “what if” scenarios to help make their predictions. For example, a company could determine the useful life of an asset by adjusting variables such as end of life dates, failure thresholds, capital costs, and time allocated for repairs. This level of insight can optimize operations, improve safety, and reduce resource expenditures.
With the right tools, companies can gain in-depth, up-to-date views of their entire network of assets to prioritize maintenance plans properly. Leverage predictive data to better forecast based on patterns and trends, driving actionable outcomes and the ability to pivot quickly.
Digital Transformation Relies on Quality Data Analytics
According to a report from Deloitte, predictive maintenance increases productivity by 25%, reduces breakdowns by 70%, and lowers maintenance costs by 25%.
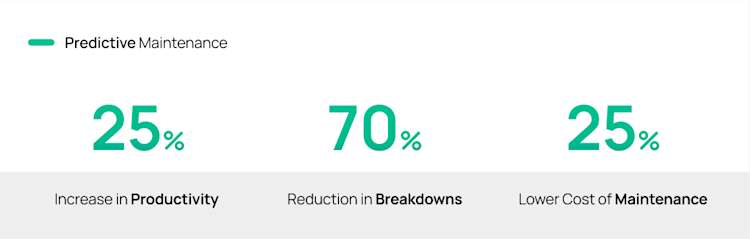
Accurate, full-picture data empowers confident decisions that eliminate unplanned downtime and catastrophic failures. Data-driven predictive maintenance plans provide precision and accuracy to prioritize and monitor assets without wasting time on redundant or unnecessary activities.
It is important to note that data quality and coverage are key. Simply put, poor data means poor decisions. Unfortunately, too many companies don’t have access to the right data, leaving them to make crucial decisions based on incomplete information. To solve this problem, companies need turnkey solutions that can collect, integrate, and analyze unprecedented amounts of high-quality data for a complete picture of asset health.
Data creates a solid foundation to build upon and scale safely to meet growing demands. Entire companies can become unified and gain visibility into a single source of truth to inform their immediate and long-term maintenance decisions. The shift from a reactive paradigm to a proactive one depends on actionable insights that make facilities more informed, effective, safer, and more productive today and into the future.