Forge a New Path: Modernizing Steel Mills with AI and Robotics
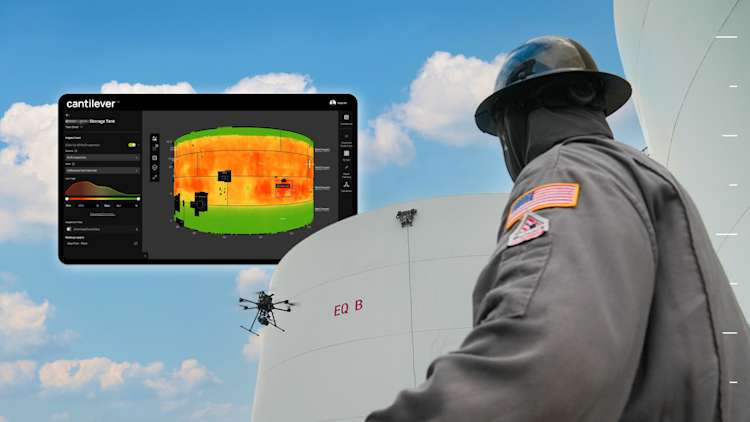
Steel manufacturing has been a critical sector of the American economy for decades. This industry has commonly been referred to as the backbone of modern industry and civilization.
Despite the steel industry’s pivotal role in the U.S. economy, the infrastructure that keeps it running is aging and increasingly failing – putting workers, steel mills, and communities at significant risk.
In general, mill managers know their equipment is in need of repair work. However, it’s extremely difficult to make a strong case for additional CapEx without clear plans and proof to justify the projected spend. Hand-drawn repair plans, manually entered data, disparate documents, and tribal knowledge simply don’t cut it.
The lack of accurate data becomes amplified as aging steel mills attempt to ramp up production to meet increasing demand while also operating on thin margins. Scaling production capacity with aging infrastructure leaves steel mills vulnerable to catastrophic failure.
Battle of the Budgets
Before you can start building repair plans and estimating costs, you must first establish a solid foundation with accurate data.
Many mills typically either perform reactive maintenance or preventive maintenance. With reactive maintenance, solutions are implemented after the damage is already done. According to the National Institute of Standards and Technology (NIST), on average, 45.7% of machinery maintenance is reactive maintenance, resulting in increased costs and unplanned downtime. Preventive maintenance is often performed on time-based intervals, which typically leads to unnecessary spending or overlooks dangerous underlying issues altogether.
Corporate-level decision makers are increasingly becoming frustrated by the pervasive gap in infrastructure data, especially as equipment failures and costs continue to climb. Large steel manufacturers can spend as much as $4,000,000,000 a year on maintenance. Allocating funds effectively is critical.
Instead, your starting point should be based on the current conditions of assets, stretching CapEx dollars while eliminating potential failures. Without an accurate baseline, it is impossible to dynamically forecast how investing money today will improve operations tomorrow.
Budget holders likely won’t approve additional spending on mill-level maintenance if there isn’t insight into the return on investment (ROI). This data gap creates a standoff between plant managers and budget holders – jeopardizing safety, uptime, and throughput.
Win Corporate Level Buy-In
Steel mills need better data to fix this escalating problem. Many mills are realizing that they won’t survive if they don’t make a change. It’s critical that companies make a shift to start embracing new technologies to change the course.
AI and robotics are transforming how mills ensure seamless operations and manage capital at every level of the organization. With better data, spending can be justified more easily, and mills can develop plans that stretch CapEx budgets, improve uptime, and drive down costs in the short and long term.
With the right technologies, mills can digitize entire fleets into a centralized operating platform, integrating important data layers for a complete understanding of asset performance. Advanced robotics can capture full-coverage data to visualize digital twins and locate precise issues with 3D modeling and mapping. Additionally, fixed sensors can be installed to continuously monitor changes in real-time.
This holistic first-order data enables better transparency and understanding across organizations while simultaneously unlocking AI-powered predictive analytics capabilities. Mills can simulate operational changes within the platform to see how certain changes can extend asset life. AI-powered analysis can quickly illustrate how assets will age and fail over the course of the next one, five, and even ten years.
Optimizing Your Mill with Data-Driven Decisions
With robot-captured data and AI-powered analysis, mills can gain clarity to make decisions faster and more confidently than ever before. For the first time, decision makers are able to understand the ROI on today’s maintenance spend as well as the tradeoffs associated with deferring maintenance.
Mills require an accurate single source of truth to win the battle of budgets. This makes it possible to build data-driven repair plans, guide operational optimizations that extend asset life, and justify CapEx allocations for the short and long term.
The mills that embrace this technology and Industry 4.0 principles are opening the door to new opportunities and brighter futures. Those that don’t will continue to lose the battle and be left behind.
Learn More
Download the 3 Blind Spots in Steel Manufacturing Ebook to discover how leading mills are eliminating risks and optimizing operations for seamless productivity.
Filed Under: