The Key to Winning the Fight Against Forced Outages
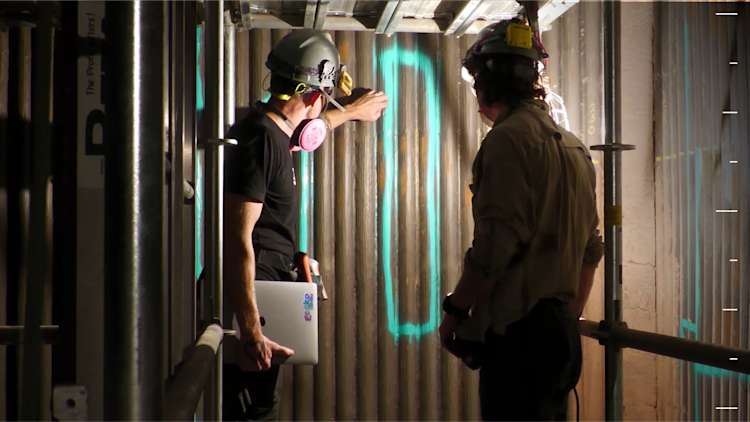
Decision-makers at power plants constantly juggle numerous priorities on an everyday basis to keep facilities running seamlessly. From maintaining budgets, predicting CapEx expenditures, ensuring safety, prioritizing maintenance activities, and maximizing workforces, to overcoming outside factors like escalating peak demand levels and unpredictable extreme weather conditions – Whew! There are several balls in the air, and not letting one drop can feel next to impossible.
Unfortunately, this complex juggling act can leave facilities feeling like an unplanned outage is always lurking around the corner. In this blog, we explain how power plants can optimize asset maintenance to confidently balance priorities and avoid forced outages.
Paying the Price for Forced Outages
A primary culprit for forced outages is boiler tube failure. According to the National Energy Technology Laboratory (NETL), more than half of forced outages at coal plants are caused by boiler tube leaks.
Every year, the number of tube leaks and forced outages that occur increases as industrial assets age. Forced outages equate to unreliable energy production and decreased revenue with operations stuck at a standstill. In addition to lost productivity and profits, the costs associated with repairs, labor, and parts often skyrocket when maintenance work is unplanned – directly impacting the bottom line.
It seems pretty simple – If a facility can eliminate boiler tube leaks, then the number of forced outages drastically reduces. However, to achieve this feat, there needs to be a shift in mindset across the power generation industry.
Around 70% of power plant leaders lack insights and data into when assets are due for maintenance, upgrades, or replacement. Without a clear picture of how assets are aging, you are simply counting down to the next asset failure by following a reactive maintenance approach.
Reactive maintenance leaves plant managers scrambling to get assets back online when a failure occurs. The Office of Energy Efficiency and Renewable Energy noted that more than 55% of maintenance resources and activities of an average facility are still reactive. While reactive maintenance can save time and investment upfront, facilities will inevitably pay the price later.
Instead of waiting until the damage is already done, some facilities implement preventive maintenance programs, performing inspections and maintenance activities on specific parts or locations of equipment based on set time intervals or machine-run-based schedules. This approach aims to extend the useful life of assets by keeping them at an acceptable level.
While this approach holds advantages over reactive programs, preventive maintenance still leaves significant gaps in coverage and accuracy. Facilities often replace assets prematurely or perform unneeded maintenance. Worse, catastrophic failures are still likely to occur due to a lack of asset health visibility. Operating on a time-based maintenance schedule and using antiquated manual inspection methods provide a very limited understanding of asset health, leaving the majority of assets completely unchecked.
The reality is that corrosion and erosion are not linear. If you don’t have insights into when and where damage is occurring, you are essentially running your equipment blind. Problem areas remain invisible, root causes stay unknown, and effective optimization is impossible.
Turn to Technology: Getting the Full Picture with an End-to-End Robotic Inspection Solution
Facilities need to shift to a predictive approach, leveraging advanced inspection technologies and data software to get the complete picture. Using robotic data collection enables facilities to get thickness measurements on nearly 100% of industrial assets – safely, efficiently, and accurately.
The full coverage, high-fidelity baseline data captured by the robots is imported into a software platform for analysis. It’s critical that this dense data becomes contextualized in order to extract actionable insights. The software platform translates millions of data points into comprehensive maps, models, and digital twins.
Digitizing industrial assets makes it easy to visualize and pinpoint specific areas that need to be immediately repaired or monitored over time. It allows facilities to see when and where failures will occur down the road – extending the useful life of the asset, maximizing budgets, ensuring reliable production, and avoiding failure.
By adjusting various parameters in the data software platform, facilities can gain visibility into how damage will progress over time to ensure issues are fixed before a failure occurs. It also gives the flexibility to model and automate different repair plans and their predicted outcomes. By fusing robotic technologies with data software platforms, facilities can eliminate guesswork to make confident decisions that drive the biggest impact.
Customer Spotlight
A power plant in West Virginia relied on manual inspection methods for many years, which left major gaps in data coverage and asset health visibility. After experiencing numerous forced outages year after year, the site decided to turn to technology to modernize its maintenance approach.
Gecko’s team worked directly with the plant to fully understand its historical data and processes. Then, the plant leveraged Cantilever™ to achieve its modernization goals. Cantilever integrates data from Gecko’s robotic systems into a software platform to analyze full-coverage asset health and make informed decisions.
The high-fidelity data was mapped into a digital twin, illustrating several areas of degradation. The plant could identify exactly which boiler tubes needed to be replaced immediately and which ones could wait until a future planned outage. This enabled proactive and timely repairs that increased plant reliability.
The data identified more than 65 boiler tubes, or over 80 square feet, with severe wastage that wasn’t detected with previous manual UT readings. The data analysis and repair plan was completed in eight hours, during the plant’s five-day planned outage. Additionally, the plant was able to complete the boiler repairs in that timeframe. Without a full picture of asset health, these problem areas would’ve remained unknown – likely leading to forced outages.
The full-coverage data analysis empowered fast, confident decision making. The entire Cantilever process, from robotic inspection and data analysis to repairs being made, was completed within the plant’s five-day planned outage.
Filed Under: